3D Printed Drone Frame
Discover the advantages and challenges of using 3D printed frames, learn from our firsthand experience, and gain valuable insights into optimizing flight performance.
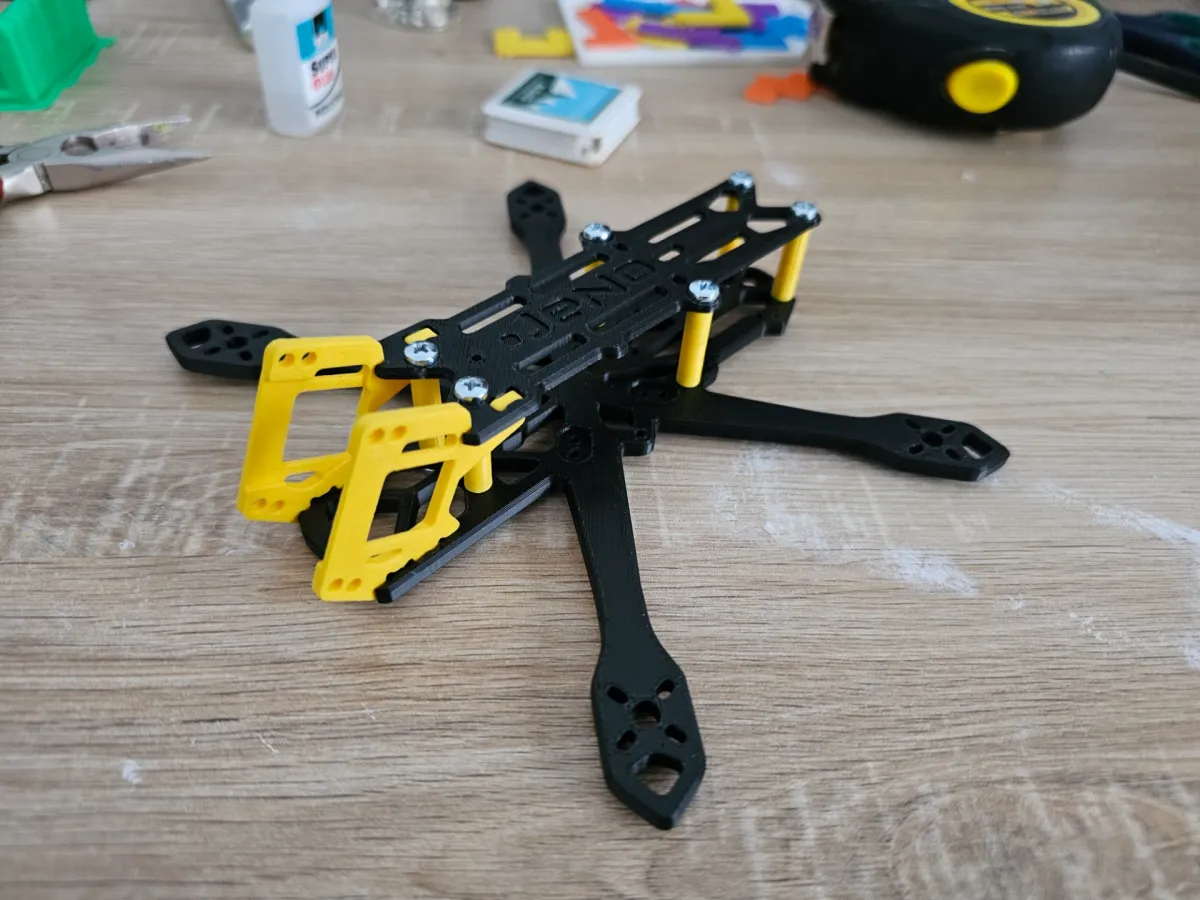
In today's fast-evolving world, technology continues to push the boundaries of innovation, offering exciting possibilities in various fields. One such groundbreaking innovation is 3D printing, a revolutionary manufacturing process that enables the creation of intricate three-dimensional objects layer by layer. From healthcare to automotive industries, 3D printing has made significant strides, but perhaps one of its most intriguing applications lies in the realm of drone technology.
As a drone enthusiast, we have always been captivated by the endless potential of these aerial machines. Their ability to soar through the skies, capturing breathtaking aerial views or delivering goods with precision, is nothing short of mesmerizing. However, what truly fascinates us is the intersection of drones with 3D printing technology. Whether you're a seasoned drone enthusiast or just curious about the possibilities of 3D printing, we invite you to join us on this exhilarating journey.
Exploring the Pros and Cons of 3D Printed Drone Frames
When it comes to building drones, selecting the right frame is paramount. In this article, we'll weigh the advantages and drawbacks of using 3D printed frames, offering a comprehensive look at what makes them both enticing and challenging.
Pros:
1. Customization: One of the most appealing aspects of 3D printed drone frames is the ability to customize them to your heart's content. With 3D printing, you're not confined to off-the-shelf designs. Instead, you can tailor the frame to suit your specific needs, whether it's adjusting dimensions, incorporating mounting points for accessories, or experimenting with unique shapes.
2. Lightweight Design: 3D printed frames are renowned for their lightweight nature. By leveraging advanced materials and intricate designs, these frames offer an optimal balance between strength and weight, crucial for achieving agile and efficient flight performance.
3. Cost-effectiveness: Compared to traditional materials like carbon fiber, 3D printing can offer a more budget-friendly alternative. With the ability to create complex geometries without incurring additional tooling costs, 3D printed frames can be an attractive option for drone builders on a budget.
4. Rapid Prototyping: 3D printing enables rapid iteration and prototyping, allowing designers to quickly test and refine their drone frame designs without the need for expensive molds or manufacturing processes. This agility can accelerate the development cycle and lead to faster innovation.
5. Integration of Complex Features: With 3D printing, intricate features such as internal channels for wiring, mounting brackets, or aerodynamic shapes can be seamlessly integrated into the frame design, enhancing functionality and performance.
6. On-demand Production: If a part breaks, assuming you already have the filament and a printer, 3D printing enables immediate on-demand production without the need to wait for shipping or visiting a physical store. Even though many retailers offer fast delivery, it’s likely not faster than (or as satisfying as) printing the part yourself.
7. More Material and Color Options: Parts can be printed in a variety of materials and colors, allowing users to select the most suitable material with optimal mechanical properties for their specific application.
Cons:
1. Strength and Durability: While 3D printed frames boast impressive lightweight designs, they may not always match the strength and durability of materials like carbon fiber. Depending on the printing process and materials used, 3D printed frames may be susceptible to damage from impacts or stress, raising concerns about their long-term reliability.
2. Vibration and Noise: Another drawback of 3D printed frames is their tendency to transmit vibrations and motor noise, which can affect flight stability and overall performance. Unlike more rigid materials, such as carbon fiber, 3D printed frames may lack the dampening properties needed to mitigate these disturbances effectively.
- Frame Resonance: 3D printed frames may exhibit resonant frequencies that coincide with the vibrations generated by the drone's motors, leading to amplified vibrations and potential instability during flight. This resonance can result in erratic behavior and compromised control, posing safety risks to the drone and surrounding environment.
- Vibration Transmission: The inherent flexibility of 3D printed materials may allow vibrations generated by the motors to propagate more freely throughout the frame. As a result, these vibrations can interfere with onboard sensors, such as accelerometers and gyroscopes, affecting the drone's ability to maintain stability and navigate accurately.
3. Flexibility: While flexibility can be advantageous in certain situations, excessive flexibility in 3D printed frames can lead to instability and poor flight characteristics. This lack of rigidity may compromise the drone's responsiveness and precision, particularly during high-speed maneuvers or windy conditions.
- Finish Quality: 3D printed frames may exhibit a rough surface finish compared to traditional manufacturing methods, which could affect aerodynamics and aesthetics. Additionally, mounting holes might need post-processing to fit well, adding time and effort to the manufacturing process.
Finding a 3D Printing Design
In the initial stages of this project, we scoured various online platforms in search of suitable drone frame designs that could be 3D printed. However, most options we encountered were either designed for larger drones or specifically intended for carbon fiber CNC fabrication. This posed a challenge as we were looking for a design that could be readily 3D printed.
After extensive searching, we stumbled upon an open-source frame called the JeNo Drone frame. While the design was promising, we encountered a hurdle: the files provided were intended for CNC machining, not 3D printing. Determined to proceed with my 3D printing endeavor, we continued my search until we came across a compatible file on MakerWorld's website based on the JeNo Drone Frame 3.
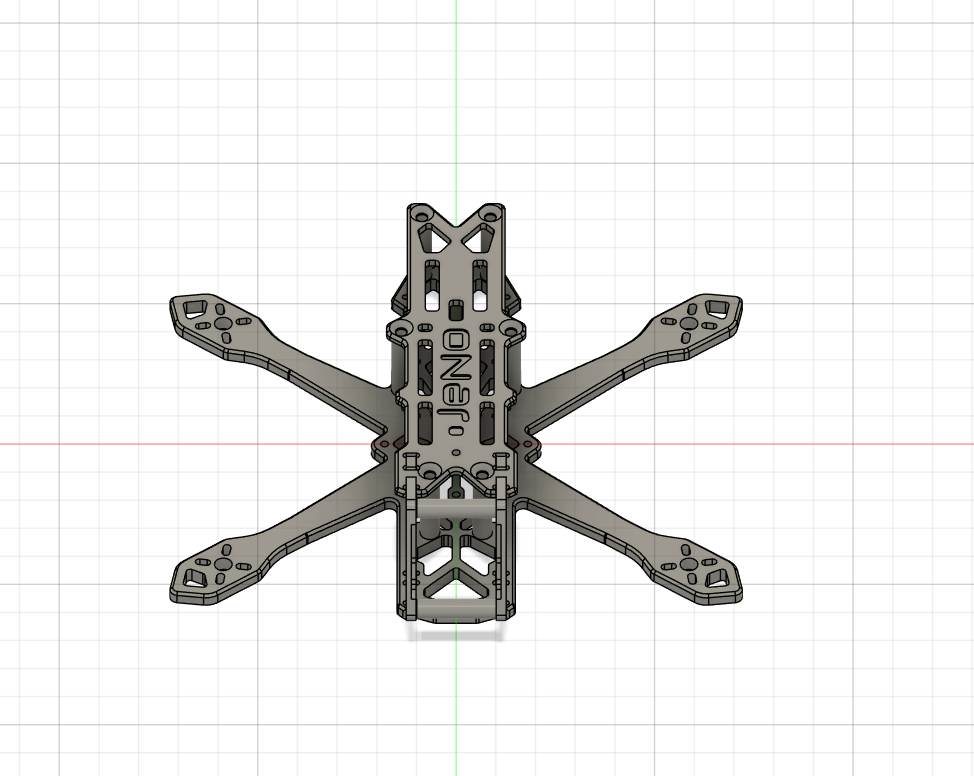
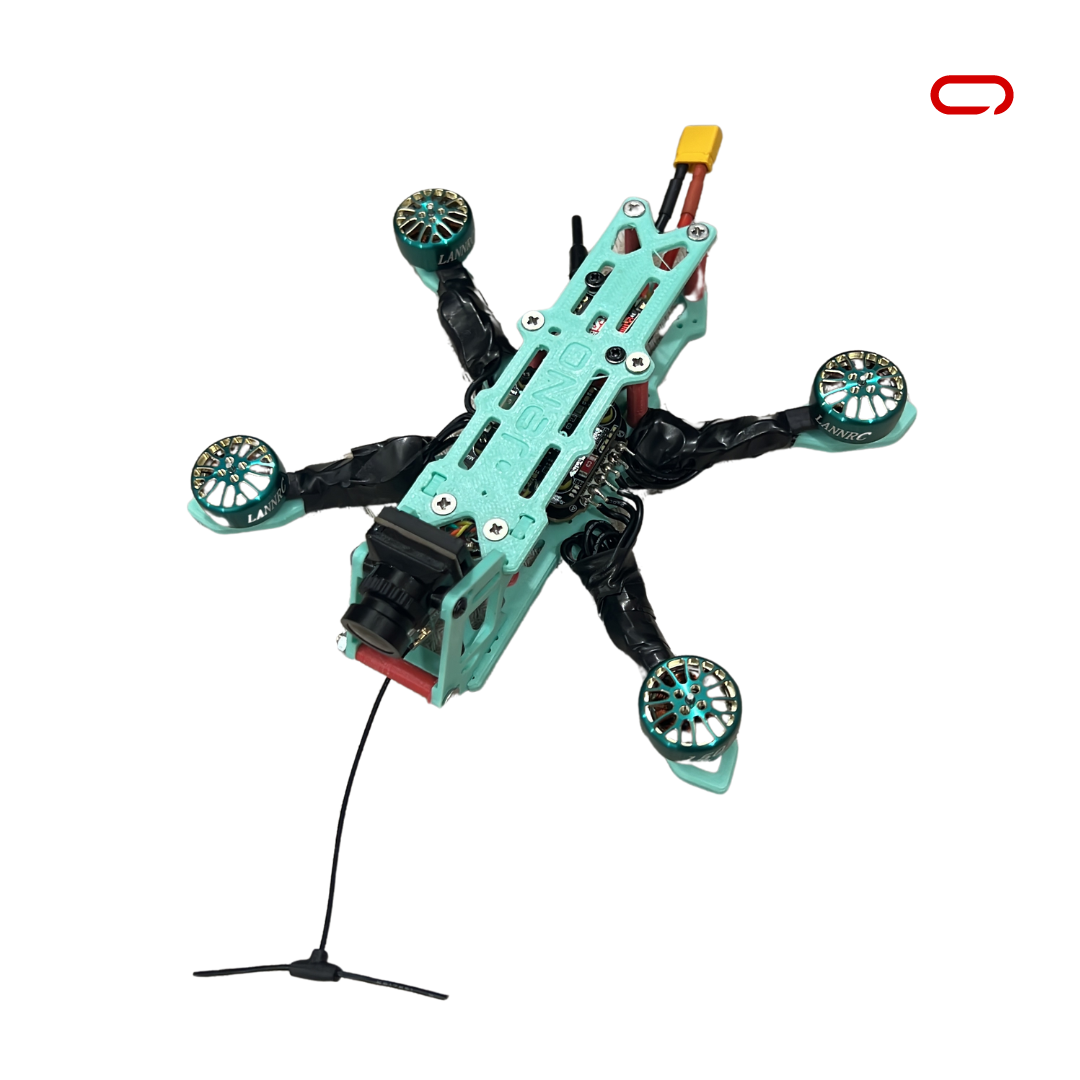
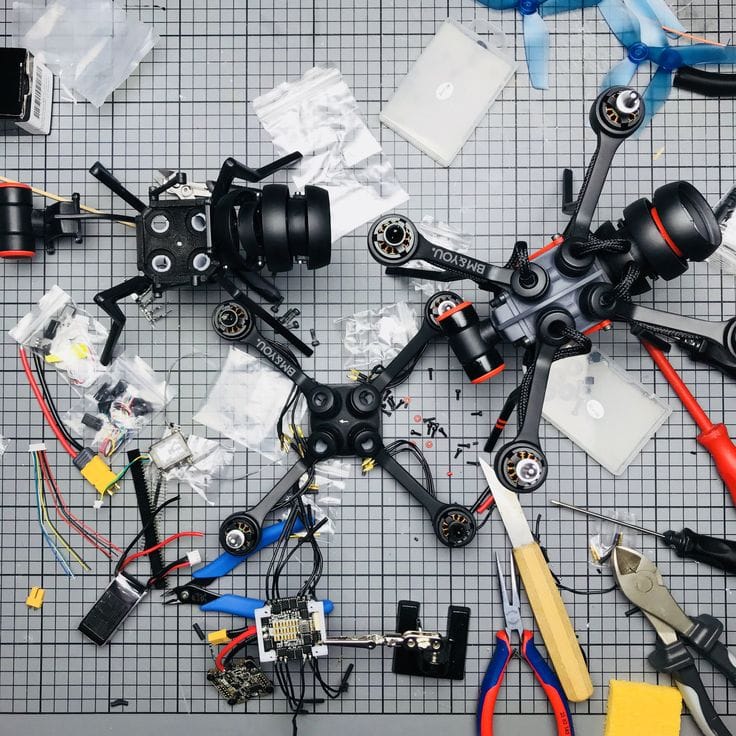
Exploring 3D Printing Techniques for Drone Frames
We went with PLA Plus material since we had it in stock. However, we discovered that PLA Plus exhibited some brittleness, underscoring the critical importance of material selection in determining the performance and durability of the drone frame.
We conducted experimentation with layer height, settling on a fine 0.10 mm layer thickness to achieve precise detailing. Complementing this, we opted for an infill density of 80%, utilizing a honeycomb infill pattern. These settings were calibrated to strike an optimal balance between structural integrity and weight reduction, crucial factors influencing the drone's flight dynamics. Despite thorough testing, we observed only marginal differences in performance between 80% and 100% infill density. Printing at the lowest temperatures and allowing ample time for the frame to cool completely before removal from the print bed significantly mitigated warping issues and notably enhanced print quality.
Additionally, it's worth noting that most of the mounting holes in the printed frame were slightly undersized, requiring screws to be screwed in instead of sliding in effortlessly. This small detail added an extra step to the assembly process but didn't significantly impact the overall functionality of the frame.
Flight Performance and Final Thoughts
Flight Experience:
Flying the drone with the 3D printed frame was an interesting experience, to say the least. Overall, it performed adequately, but it fell short of perfection. The vibration issues were clear and noticeable, affecting the drone's stability and maneuverability, especially when flying around obstacles. The most concerning aspect was the erratic behavior exhibited by the drone upon small impacts or collisions. The frame's noticeable flexing and shaking only added to the challenges encountered during flight. Sadly, the initial crash resulted in the frame to break, highlighting its susceptibility to impact and limited durability. Would we recommend it? Well, for its color options and the novelty of customization, perhaps. However, for reliability and durability, we hesitate to offer a resounding endorsement.
Comparison with Commercial Models:
Comparing our 3D Printed frame with commercial models, particularly those constructed from carbon fiber, revealed a night and day difference in performance. The carbon fiber model exhibited superior stability, maneuverability, and endurance. In contrast, our 3D-printed drone struggled to match these standards. While it was capable of flight, it required extensive tuning to address vibration and noise issues—a process that often felt like an exercise in trial and error. Certain settings even triggered excessive frame vibrations, resulting in motor shutdowns—an issue we suspect may be related to frame resonance.
Reflections on 3D Printing Technology:
Utilizing 3D printing technology for drone frame construction was an eye-opening experience, providing a glimpse into the potential and limitations of additive manufacturing. It was undeniably satisfying to create a custom drone from the comfort of home with just a few hours of printing. However, it's crucial to acknowledge the inherent trade-offs. While suitable for hobbyist use and experimentation with budget-friendly builds, 3D-printed frames lack the robustness and reliability required for real-world applications. The need for extensive tuning and the fragility of the frame underscored the importance of ongoing innovation in this field. It could be that PETG, ABS or even CF filament would address these issues.
In conclusion, our journey with 3D printing technology for drone frame construction was both enlightening and humbling. While it may not yet match the performance and dependability of traditional materials like carbon fiber, it undoubtedly holds promise for future innovation and exploration in the realm of drone customization and personalization.